Materialdisposition in Zeiten knapper Ressourcen
Fragile Supply Chains bleiben auf absehbare Zeit eine gravierende Herausforderung für die Materialdisposition der fertigenden Industrie. Wie können Unternehmen bei mangelhafter Versorgungslange dennoch eine bestmögliche Lieferbereitschaft für eine hohe Kundenzufriedenheit realisieren? Die Disposition von zu beschaffenden und zu fertigenden Produkten braucht hierfür Tools, um selbst bei tiefsten Stücklisten schnelle Ad-hoc-Erkenntnisse zu kritischen Artikeln zu erlangen.
Disponenten stehen heute vor einer Vielzahl komplexer Probleme, die sie mit konventioneller Planbedarfsermittlung nicht mehr lösen können. Seit der Corona-Pandemie, spätestens aber mit dem Ausbruch des Krieges in der Ukraine, greift in vielen Industriebetrieben eine bisher nicht gekannte Materialknappheit um sich: Die Lieferanten der fertigenden Unternehmen können nicht mehr wie gewohnt jedes erdenkliche Vorprodukt fristgerecht und in den gewünschten Mengen liefern. Sie sind aufgrund der auch bei ihnen fehlenden Ressourcen gezwungen, Bedarfe abzusagen oder nur noch in kleineren Losen oder auch deutlich teurer zu bedienen. Das führt in der fertigenden Industrie jeder Wertschöpfungsstufe zu dem Problem, dass für unzählige Fertigprodukte einzelne Stücklistenkomponenten fehlen und man selbst auch nur begrenzte Mengen an Fertigwaren ausliefern kann. In dieser Situation ist es entscheidend, genau zu wissen, welche Mengen von welchen Komponenten man tatsächlich benötigt. So kann man zumindest die dringendsten Bedarfe der eigenen Kunden bedienen und vor allem die zu geringen Mengen an Zukaufmaterialien für die Produktion der deckungsbeitragsstärksten Fertigprodukte verwenden.
Die Aufgabe scheint einfach. Auf den ersten Blick errechnet jeder MRP-Planungslauf eines ERP-Systemen genau diese Materialbedarfsmengen. Bei genauerer Betrachtung stellt man jedoch fest, dass die in einem MRP-Lauf ermittelten Mengen an Halbfertigartikeln, Rohmaterialien und Zukaufteilen um einiges größer sind, als die akut tatsächlich benötigten Mengen. Die Ursache dafür liegt in einer ganzen Reihe von materialnummernspezifischen Dispositionsparametern und Dispositionseinstellungen, die bei einem MRP-Lauf berücksichtigt werden und dazu führen, dass die kurzfristig benötigten Materialmengen deutlich aufgeblasen werden. Die Konsequenzen, die sich jedoch aus der Berücksichtigung von Sicherheitsbeständen, Mindestbestellmengen und Mindestfertigungslosen sowie Rundungslosgrößen ergeben, macht ein kleines Rechenbeispiel (Abb. 1) deutlich: Anstatt des akuten Bedarfs von 4 Reifen und 28 Schrauben würde eine normale Materialbedarfsrechnung 75 Reifen und 750 Schrauben als Bestellbedarf ermitteln.
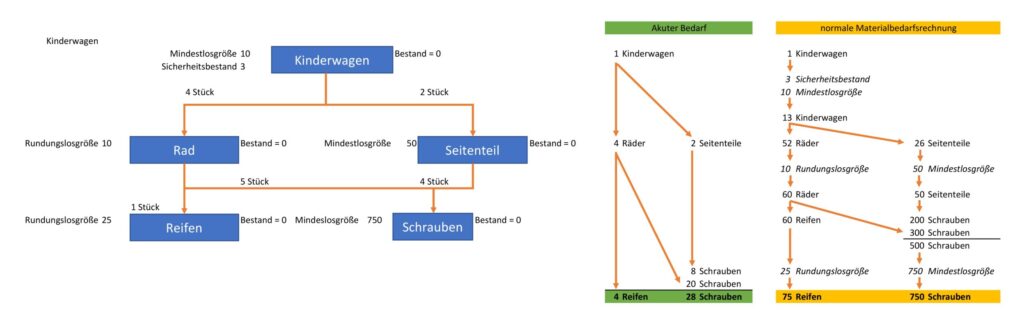
Die als vermeintlich notwendig ermittelten Bedarfe an Komponenten können sich noch weiter erhöhen, wenn in die Berechnung nicht nur vorhandene Kundenaufträge einfließen, sondern auch Planprimärbedarfe aus statistischen Absatzprognosen und Vertriebsplänen.
Den reinen Bedarf ermitteln
Die ermittelten Mengen an zu bestellenden und zu fertigenden Artikeln sind also Ergebnis von komplexen Kalkulationen , die in der Regel viele tausend Materialnummern berücksichtigen. Solch hohe Abstraktionsgrade mit Regelwerken für hunderte von Dispositionsparametern und zahlreichen Optimierungsalgorithmen verschleiern den für den real bestehenden Auftragsbestand notwendigen reinen Materialbedarf erheblich.
„Damit zeigt sich deutlich, dass über klassische Materialbedarfsrechnungen ermittelte Bedarfe an Fertigungs- und Beschaffungsteilen weit über den echten Bedarf an diese Teilen hinausgreifen“, erklärt Andreas Capellmann, Geschäftsführer der SCT Supply Chain Technologies GmbH (Bild rechts). Je tiefer und breiter die Stücklisten und je mehr Fertigprodukte, desto schwerer und aufwändiger ist es, den echten Komponentenbedarf zu ermitteln. Die Bedarfsmengen jeder Stücklistenstufe manuell zu überprüfen und dabei die zuvor beschriebenen Dispositionsparameter wegzurechnen, ist bei oftmals vielen tausenden zu disponierenden Artikeln schlichtweg unmöglich!
SCT hat deshalb sein Dispositionsmanagementsystem DISKOVER um die strategischen Funktionen des neuen Critical Parts Information Systems, kurz CPIS, erweitert. Mit dieser Funktion lassen sich die tatsächlichen Komponentenbedarfe, befreit von Verzerrungsgrößen wie Sicherheitsbestand, Mindestlosgrößen, Mindestbestellmengen und nicht kundenauftragsverursachten Planprimärbedarfen ermitteln. „Auf Knopfdruck können Disponentinnen und Disponenten jeweils einzelne dieser Einflussgrößen deaktivieren oder aktivieren und damit einen präzisen Blick auf die sich so ändernden Rahmenbedingungen schaffen – bis hin zum Blick auf den nackten Bedarf für die real existierenden Auftragsvolumina – und das über alle Fertigungsstufen hinweg“, so Capellmann.
Und weiter: „CPIS ist eine neue Krisenmanagementfunktion unseres Dispositionsmanagementsystems DISKOVER, die bei kritischen Artikeln zum Einsatz kommt – also Komponenten, die knapp sind und deshalb nicht wie gewohnt zeitig in den eigentlich erforderlichen normalen Losen geordert werden können“
Randbedingungen automatisiert ausblenden
„Bislang war bei der Artikelbedarfsdisposition nicht die verfügbare Menge an Komponenten die kritische Größe, sondern vielmehr der Faktor Zeit. Früher ging es vornehmlich darum, den optimalen Zeitpunkt dafür zu bestimmen, wann was und wieviel davon bestellt oder gefertigt werden muss, damit die Lieferbereitschaft hoch und die Bestände gering bleiben. Heute hingegen ist der kritische Größe, überhaupt Material zu bekommen, um die bestehenden Aufträge bedienen zu können“, fasst Capellmann die derzeitigen Rahmenbedingungen für die industrielle Fertigung zusammen. Der Einsatz der CPIS-Funktion von DISKOVER versetzt Unternehmen schlussendlich in die Lage, mit wenigen Klicks eine belastbare Grundlage für auftragsbezogene Disposition und Allokation kritischer Artikel zu schaffen. Sie können so deutlich schneller entscheiden, welche realen Kundenbedarfe sie schlussendlich erfüllen können und wollen und in welchem Endprodukt kritische Artikel den meisten Umsatz oder Deckungsbeitrag generieren.
Critical Parts tagesaktuell identifizieren
Doch so praktisch das Tool auch ist: Es sollte nur für diese Notfällen zum Einsatz kommen. „Faktoren wie Sicherheitsbestände und Mindestlosgrößen sind einfach notwendig für einen sicheren Betriebsablauf. Das kann man nicht auf Dauer komplett ausblenden“, meint Capellmann.
Fazit: Die CPIS-Funktion von DISKOVER macht auf Komponentenebene transparent, von welchen kritischen Artikeln der Umsatz auf der Zeitschiene – üblicherweise im Wochenraster –wie stark abhängt und liefert zuverlässige Auswertungen darüber, für welche Aufträge sie bei fehlenden Beständen am wirtschaftlichsten eingesetzt werden können.